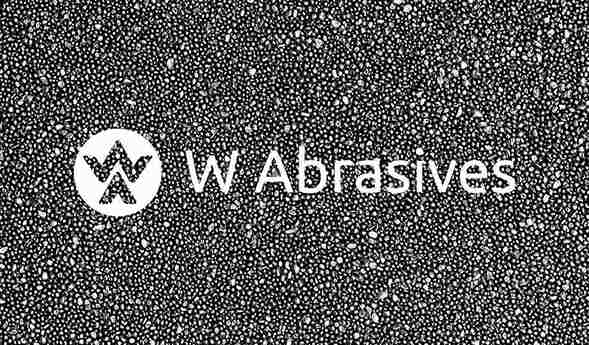
Abrasive blasting is one of the most versatile surface engineering processes. It uses the abrasive power of metallic abrasives, such as grit, spherical shot or stainless steel shot, to precisely shape and clean the surface of various materials. In this article, we will take a closer look at this fascinating process, its applications and the benefits it brings to various industries.
Abrasive blasting is used in many areas of surface engineering. It can be used to remove dirt, rust, paint and other coatings that deposit on metal surfaces. In addition, this process enables precise shaping and smoothing of the surface, which is particularly important in the production of components with high technical requirements.
Abrasive machining - basics
Abrasive machining is the process of removing material from a surface using abrasive particles. It can be carried out in various ways, such as grinding, polishing, milling or planing. Abrasive blasting is one of the abrasive processing techniques that uses the kinetic energy of metallic abrasives, including steel abrasives and stainless steel abrasives, to achieve the desired effect.
How does abrasive blasting work?
Abrasive blasting consists in directing a stream of metallic abrasives along the surface of the workpiece using special devices, such as blasting machines. The stream of abrasives is generated by a pneumatic or hydraulic system and directed at the surface at the right angle and with the right force.
When abrasive particles, such as cast steel shot or spherical steel shot, hit the surface of the material, an abrasive effect occurs that removes layers of material, cleans the surface, and shapes the detail. The impact force of the abrasive particles and their shape and size are crucial to achieve the desired machining result.
Abrasive blasting applications
Abrasive blasting is widely used in many industries. Here are some examples:
Metallurgical industry
In the metallurgical industry, abrasive blasting is used to remove oxidized layers, rust, paint or other contaminants from the surface of metal components. This process, using high-quality abrasives, such as cast steel and stainless steel abrasives, is extremely effective, allowing the surface to be prepared for the next stages of production, such as painting, welding or hardening.
Foundry
In foundry, abrasive blasting is used to clean and smooth the surface of castings. Removing excess material, impurities or hard shells with abrasives such as broken grit or ball grit results in finished, aesthetic and functional products.
Aerospace and automotive industry
In these industries, abrasive blasting is used to clean, smooth and strengthen the surfaces of various components such as turbines, impellers, cylinders and crankshafts. This process, using cast steel and stainless steel abrasives, allows to improve the strength and durability of components and increase their efficiency.
Benefits of using abrasive blasting
Abrasive blasting has many advantages over other surface treatment techniques. Here are some of them:
- Effective cleaning of the surface from various types of impurities and oxidized layers.
- Precise detail shaping, keeping sharp edges and geometric details.
- The impact force and the shape of the abrasive particles can be adjusted, which allows the process to be adapted to specific requirements.
- The ability to automate the process, which contributes to increased efficiency and precision.
- Reduced risk of component damage or deformation compared to some other machining techniques.
Summary
Abrasive blasting is a versatile and effective surface treatment process that uses the abrasive power of metallic abrasives. Thanks to this process, it is possible to precisely shape the surface of various materials in a controlled and effective manner. The use of abrasive blasting is found in various industries, and the benefits of this process are numerous. Therefore, this technology plays an important role in improving the quality and functionality of products and in increasing production efficiency.