Obróbka strumieniowo-ścierna, choć niezbędna w wielu gałęziach przemysłu, może generować znaczne koszty operacyjne. Na szczęście istnieje wiele sposobów, aby te koszty zredukować, zachowując przy tym wysoką jakość obróbki. W tym artykule omówimy kluczowe strategie, które pozwolą firmom na oszczędności w obróbce strumieniowej, koncentrując się na wyborze ścierniw, konserwacji sprzętu, optymalizacji procesów oraz szkoleniu pracowników.
Wybór odpowiednich ścierniw
Wybór odpowiednich ścierniw jest jednym z najważniejszych czynników wpływających na koszty obróbki. Wiele firm kieruje się wyłącznie ceną zakupu ścierniwa, co jest błędem. Prace bazujące na tanich ścierniwach mogą prowadzić do wyższych kosztów w dłuższej perspektywie, jeśli trwałość tych ścierniw jest niska lub jeśli powodują one nadmierne zużycie sprzętu.
Aby zmniejszyć koszty, warto inwestować w ścierniwa o wyższej jakości, które charakteryzują się dłuższą żywotnością i mniejszą tendencją do generowania pyłu. Materiały takie jak kulki szklane, granulat plastikowy czy staliwo mogą być droższe na początku, ale ich większa wydajność i trwałość pozwalają na zmniejszenie kosztów obróbki w dłuższym czasie.
Regularna konserwacja sprzętu
Sprzęt do obróbki strumieniowo-ściernej podlega intensywnej eksploatacji, co prowadzi do jego zużycia. Regularna konserwacja jest kluczem do zapobiegania awariom, które mogą być kosztowne zarówno pod względem napraw, jak i przestojów produkcyjnych.
Planowane przeglądy i konserwacje pozwalają na wczesne wykrywanie i usuwanie usterek, zanim doprowadzą one do poważniejszych problemów. Efektywne zarządzanie obróbką ścierną wymaga stałego monitorowania stanu techni\cznego sprzętu, w tym dysz, filtrów, przewodów oraz silników. Regularna wymiana zużytych elementów, takich jak uszczelki czy dysze, może znacznie przedłużyć żywotność całego systemu.
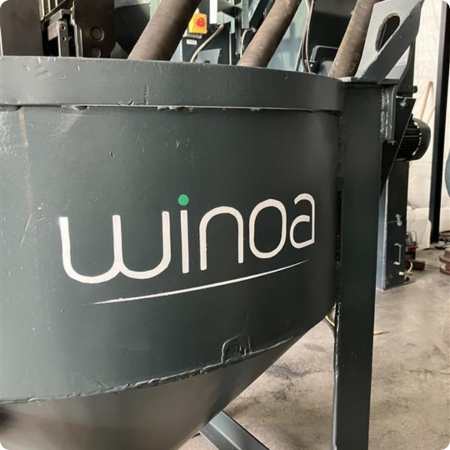
Optymalizacja procesów ściernych
Kolejnym krokiem do obniżenia kosztów jest optymalizacja samego procesu obróbki. W tym celu warto przeanalizować i dostosować parametry takie jak ciśnienie powietrza, prędkość strumienia, kąt nachylenia dyszy oraz ilość używanego ścierniwa.
Często stosowanym rozwiązaniem jest automatyzacja procesów, która pozwala na precyzyjne kontrolowanie i optymalizację parametrów obróbki. Dzięki temu można zmniejszyć zużycie materiałów i energii, a także zredukować czas potrzebny na obróbkę jednej sztuki, co bezpośrednio przekłada się na zmniejszenie kosztów obróbki.
Szkolenie pracowników
Nie można zapominać o roli pracowników w procesie obróbki strumieniowo-ściernej. Nawet najlepszy sprzęt i materiały nie zapewnią oczekiwanych oszczędności, jeśli nie będą odpowiednio użytkowane. Regularne szkolenia z zakresu obsługi maszyn, konserwacji oraz bezpieczeństwa pracy są niezbędne, aby pracownicy mogli efektywnie wykorzystywać dostępne zasoby.
Szkolenia powinny obejmować zarówno teoretyczne, jak i praktyczne aspekty pracy, w tym umiejętność rozpoznawania oznak zużycia sprzętu oraz właściwego doboru parametrów obróbki. Optymalizacja procesów ściernych nie jest możliwa bez kompetentnej kadry, która potrafi w pełni wykorzystać potencjał dostępnych technologii.
Efektywne zarządzanie zapasami ścierniw oraz bieżące monitorowanie ich zużycia to kluczowe elementy w procesie redukcji kosztów. Automatyczne systemy monitorujące pozwalają na dokładne śledzenie ilości używanych materiałów, co zapobiega nadmiernemu zużyciu oraz niepotrzebnym zakupom.
Warto także wprowadzić system rotacji zapasów, aby ścierniwa były zużywane zgodnie z zasadą FIFO (first in, first out), co minimalizuje ryzyko przeterminowania się materiałów. Regularne analizy zużycia pozwalają również na identyfikację obszarów, w których można wprowadzić dodatkowe oszczędności, na przykład przez modyfikację procesów lub zmianę dostawcy.