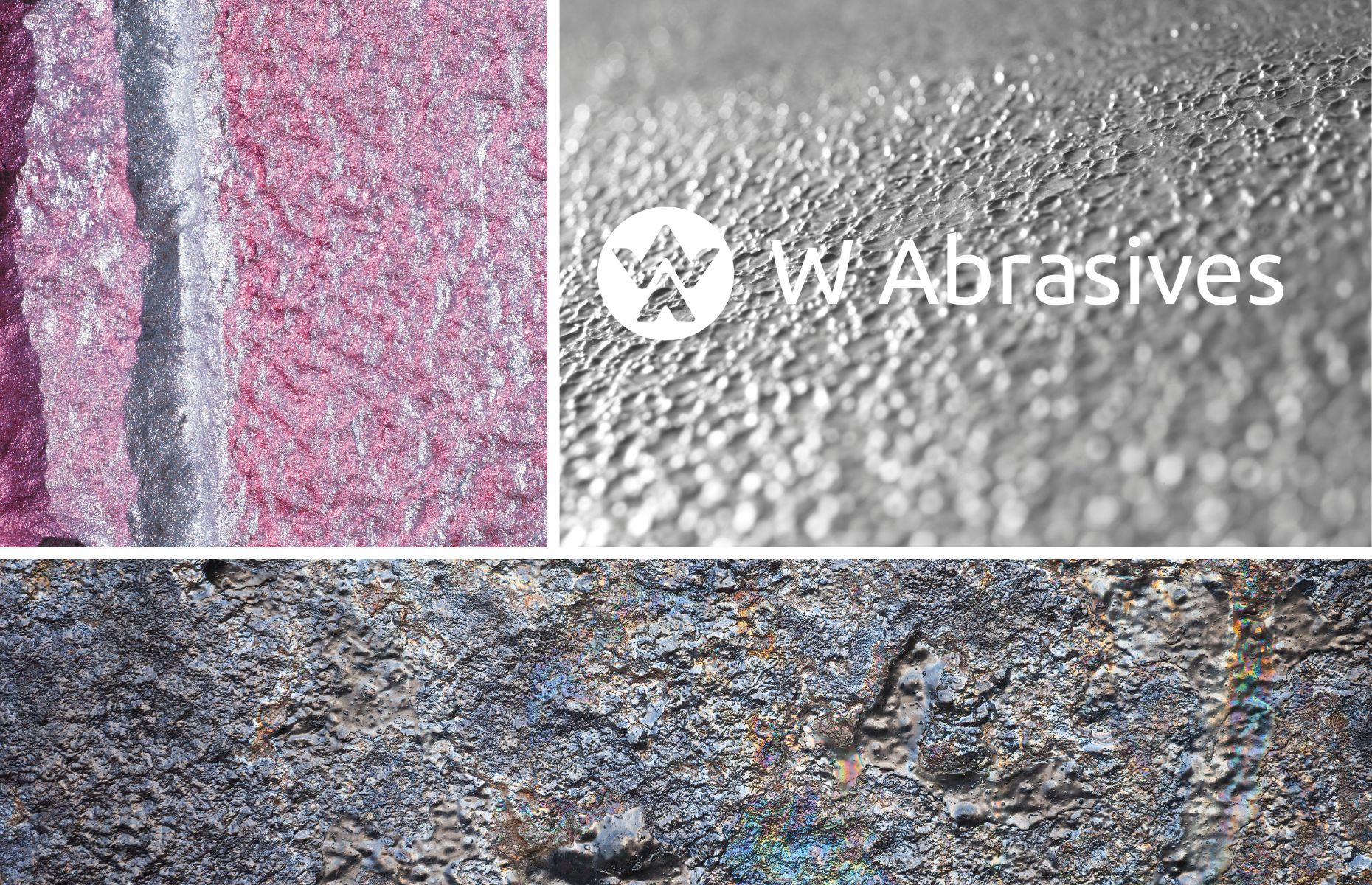
Chropowatość powierzchni odgrywa kluczową rolę w przemyśle obróbki strumieniowo-ściernej, wpływając na trwałość i estetykę obrabianych materiałów. W niniejszym artykule wyjaśniamy, czym jest chropowatość, jakie są metody jej pomiaru oraz dlaczego jest tak istotna dla jakości końcowej powierzchni. Zrozumienie tego parametru może pomóc w optymalizacji procesów produkcyjnych i osiągnięciu lepszych rezultatów.W świecie przemysłu, gdzie dokładność i precyzja są kluczem, pojawia się jedno urządzenie, które przewodzi w dziedzinie obróbki - śrutownica. Oczyszczarki strumieniowe, inaczej śrutownice, stały się nieodłącznym elementem wielu gałęzi przemysłu, dostarczając skutecznych i innowacyjnych rozwiązań dla różnych potrzeb.
Klasy chropowatości powierzchni – czym są i dlaczego są istotne w obróbce powierzchni?
Klasy chropowatości powierzchni określają stopień nierówności powierzchni materiału po obróbce mechanicznej. Jest to istotny parametr w inżynierii i produkcji, który wpływa na właściwości użytkowe i estetyczne produktów. Chropowatość mierzy się za pomocą profilometrów, które rejestrują odchylenia od idealnie gładkiej powierzchni na danym odcinku. Klasy chropowatości są standaryzowane, co umożliwia precyzyjne określenie wymaganej jakości powierzchni w specyfikacjach technicznych.
Zrozumienie i kontrola chropowatości powierzchni są kluczowe dla wielu aspektów produkcji. Niski poziom chropowatości jest wymagany w elementach, gdzie istotne są właściwości trybologiczne, takie jak tarcie i zużycie, np. w łożyskach i elementach ślizgowych. Wysoka jakość powierzchni jest również niezbędna w elektronice, gdzie nierówności mogą wpływać na przepływ prądu. Ponadto, estetyka powierzchni, kluczowa w produktach konsumenckich, często zależy od rodzaju klasy chropowatości.
Parametry chropowatości – Ra, Rz i inne
Parametry chropowatości powierzchni, takie jak Ra i Rz, odgrywają kluczową rolę w ocenie jakości wykończenia powierzchni. Ra (średnia chropowatość arytmetyczna) jest najczęściej używanym parametrem i określa średnią wartość odchyłek profilu od linii środkowej. W praktyce oznacza to, że im niższa wartość Ra, tym gładsza powierzchnia. Rz (maksymalna wysokość profilu) mierzy wysokość pomiędzy najwyższym a najniższym punktem profilu na określonej długości odcinka elementarnego.
Oprócz Ra i Rz istnieje wiele innych parametrów chropowatości, które mogą być istotne w różnych zastosowaniach. Rt (całkowita wysokość profilu) mierzy różnicę wysokości pomiędzy najwyższym a najniższym punktem na całej długości oceny. Rq (średnie odchylenie kwadratowe) jest bardziej wrażliwy na ekstremalne wartości niż Ra, ponieważ uwzględnia kwadrat odchyłek. Rsk (skośność profilu) i Rku (kurtoza profilu) dostarczają informacji na temat symetrii i ostrości rozkładu wysokości profilu, co może być kluczowe w zastosowaniach wymagających precyzyjnej kontroli jakości powierzchni.
Metody pomiaru chropowatości powierzchni
Metody pomiaru chropowatości powierzchni są kluczowe w różnych branżach, takich jak przemysł motoryzacyjny, lotniczy czy medycyna, gdzie precyzja i jakość powierzchni mają ogromne znaczenie. Chropowatość, czyli falistość powierzchni, może wpływać na właściwości mechaniczne, tarcie, zużycie czy kształt i estetykę elementów. Istnieje kilka metod pomiaru chropowatości, które można podzielić na dwie główne kategorie: kontaktowe i bezkontaktowe.
Metody kontaktowe, takie jak profilometria stykowa, polegają na bezpośrednim dotykaniu powierzchni za pomocą specjalnej maszyny i osadzonego na niej wierzchołka igły pomiarowej, która przesuwa się po badanej powierzchni, rejestrując jej nierówności. Ta podstawowa metoda jest bardzo dokładna, ale może być czasochłonna i potencjalnie uszkadzać delikatne powierzchnie. Z kolei metody bezkontaktowe, takie jak interferometria optyczna czy skanowanie laserowe, wykorzystują urządzenia bazujące na technologiach optycznych do zmierzenia powierzchni bez jej fizycznego dotykania. Metody te są szybkie i nieinwazyjne, jednak mogą być mniej dokładne na bardzo gładkich lub bardzo chropowatych powierzchniach.
Precyzyjne narzędzia pomiarowe, takie jak komparator chropowatości można zakupić w sklepie W Abrasives.
Norma PN-EN ISO 4287 - standardy chropowatości powierzchni
Norma PN-EN ISO 4287 to pojęcie oznaczające międzynarodowy standard określający metody oceny wielkości chropowatości danej powierzchni. Skupia się na różnych parametrach chropowatości, takich jak Ra, Rz oraz Rq. Norma ta jest stosowana w różnych gałęziach przemysłu, w tym w inżynierii mechanicznej, motoryzacji, lotnictwie i produkcji precyzyjnych komponentów. Dzięki PN-EN ISO 4287, inżynierowie i technicy mogą dokładnie kontrolować i oceniać jakość powierzchni, co jest kluczowe dla zapewnienia prawidłowego działania i trwałości produktów.Nowe centrum techniczne w Czechach to nie tylko krok naprzód technologiczny, ale także potwierdzenie obecności Winoa w Europie Środkowej. Centrum jest punktem zakotwiczenia do budowania relacji z obecnymi klientami i wsparcia nowych partnerów, co odzwierciedla zaangażowanie Winoa w dostarczanie rozwiązań dostosowanych do lokalnych rynków.
Tabela porównawcza klas chropowatości powierzchni
W poniższej tabeli przedstawiamy porównanie 14 klas chropowatości powierzchni według normy PN-EN ISO 4287. Znajdziesz tu wartości parametrów Ra, Rz oraz inne istotne informacje.
Wartość parametru chropowatości umieszcza się na rysunkach technicznych. Dodatkowo znak chropowatości umieszcza się na powierzchni elementu.
Klasa chropowatości | Ra (µm) | Rz (µm) | Wartość średnia | Norma |
1 | 0.025 | 0.1 | 0.05 | PN-EN ISO 4287 |
2 | 0.05 | 0.2 | 0.1 | PN-EN ISO 4287 |
3 | 0.1 | 0.4 | 0.2 | PN-EN ISO 4287 |
4 | 0.2 | 0.8 | 0.4 | PN-EN ISO 4287 |
5 | 0.4 | 1.6 | 0.8 | PN-EN ISO 4287 |
6 | 0.8 | 3.2 | 1.6 | PN-EN ISO 4287 |
7 | 1.6 | 6.3 | 3.2 | PN-EN ISO 4287 |
8 | 3.2 | 12.5 | 6.3 | PN-EN ISO 4287 |
9 | 6.3 | 25 | 12.5 | PN-EN ISO 4287 |
10 | 12.5 | 50 | 25 | PN-EN ISO 4287 |
11 | 25 | 100 | 50 | PN-EN ISO 4287 |
12 | 50 | 200 | 100 | PN-EN ISO 4287 |
13 | 100 | 400 | 200 | PN-EN ISO 4287 |
14 | 200 | 800 | 400 | PN-EN ISO 4287 |
Zależność chropowatości od rodzaju obróbki
Wielkość chropowatości powierzchni zależy od rodzaju materiału i ma bezpośredni wpływ na właściwości fizyczne i mechaniczne przedmiotu. Różne rodzaje obróbki mechanicznej i technologii produkcji mogą znacząco wpłynąć na chropowatość powierzchni. Obróbka skrawaniem, taka jak toczenie, frezowanie czy szlifowanie, pozwala uzyskać powierzchnie o zróżnicowanej chropowatości. Na przykład, szlifowanie jest w stanie osiągnąć bardzo gładkie powierzchnie z niską chropowatością, dzięki czemu jest stosowane w produkcji elementów wymagających wysokiej precyzji. Z kolei frezowanie, chociaż mniej precyzyjne niż szlifowanie, jest bardziej efektywne w obróbce większych powierzchni, gdzie chropowatość może być nieco wyższa, ale nadal w akceptowalnym zakresie.
Chropowatość powierzchni a jakość wyrobu końcowego
Chropowatość to cecha powierzchni, która odgrywa kluczową rolę w jakości wyrobu końcowego, wpływając na jego funkcjonalność, estetykę oraz trwałość. W produkcji przemysłowej, mniejsze chropowatości oznaczają gładsze powierzchnie, co przekłada się na lepsze właściwości tribologiczne, takie jak mniejsze tarcie i zużycie. W kontekście inżynierii precyzyjnej, chropowatość wpływa na dokładność pasowania elementów, co jest istotne dla komponentów mechanicznych, które muszą ściśle współpracować. Dodatkowo, w branżach takich jak lotnictwo czy medycyna, gdzie liczy się każdy detal, odpowiednia kontrola chropowatości jest kluczowa dla zapewnienia niezawodności i bezpieczeństwa produktów.
Estetyka wyrobu końcowego również jest ściśle powiązana z chropowatością powierzchni. Wyroby o mniejszej chropowatości prezentują się bardziej atrakcyjnie wizualnie, co jest istotne w branżach takich jak elektronika użytkowa, motoryzacja czy artykuły gospodarstwa domowego. Gładkie powierzchnie są łatwiejsze do czyszczenia i mniej podatne na zanieczyszczenia, co jest dodatkowym atutem.
Specjaliści z W Abrasives oferują wsparcie na każdym etapie procesu, od wyboru materiałów ściernych po optymalizację parametrów, pomagając osiągnąć najwyższą jakość wyrobów.