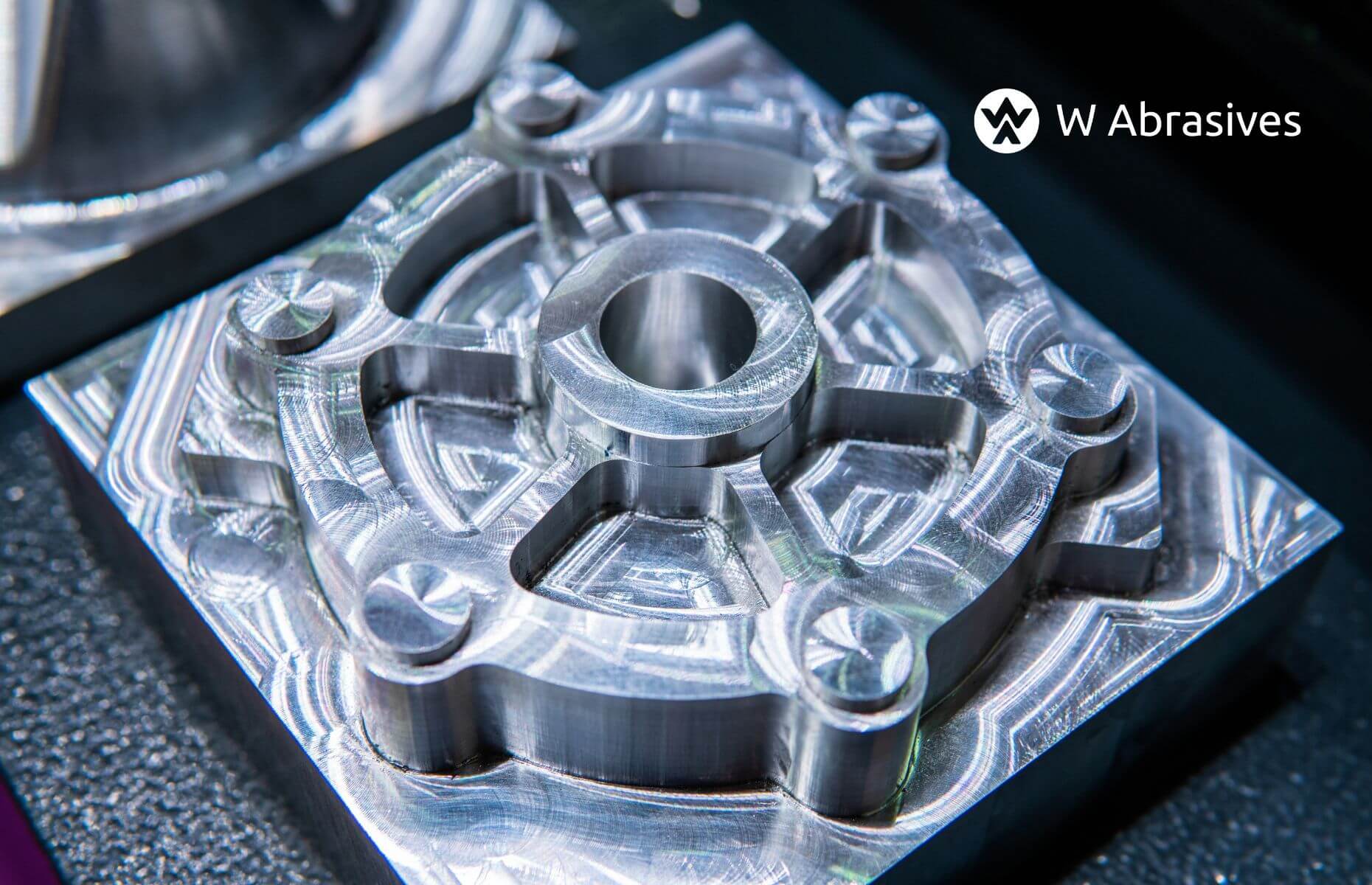
Cylindry magnetyczne w śrutowaniu: innowacja dla odlewni
W nowoczesnym przemyśle coraz większe znaczenie zyskuje proces szkiełkowania. To niepozorne działanie, będące integralną częścią produkcji różnorodnych produktów, od elementów elektronicznych po precyzyjne narzędzia, stanowi istotny krok w doskonaleniu jakości i trwałości materiałów. W centrum tego procesu tkwi rola szklanych mikrokulek - ścierniw, które pełnią kluczową funkcję w kształtowaniu właściwości końcowego produktu.
Ścierniwo do szkiełkowania - profesjonalne ścierniwo wielokrotnego użytku!
Ścierniwo to materiał służący do szlifowania, polerowania i obróbki powierzchni, a jego różnorodne rodzaje oraz zastosowania stanowią kluczowy element procesu obróbki strumieniowo-ściernej. Szkiełkowanie to proces wykorzystujący w charakterze ścierniwa szklane mikrokulki, które ze względu na swoje doskonałe właściwości ściernotwórcze sprawdzają się w obróbce różnych rodzajów metali. Warto jednak pamiętać, że szkiełkować możemy także elementy wykonane z metali nieżelaznych, stali nierdzewnej, tworzyw sztucznych itp.
Dzięki swojej twardości i jednorodnej strukturze kulki szklane umożliwiają precyzyjne kształtowanie obrabianej powierzchni, co sprawia, że są szczególnie cenione chociażby w przemyśle związanym z mikroelektroniką, przy produkcji precyzyjnych elementów mechanicznych oraz w szklarstwie artystycznym.
Mikrokulki szklane z reguły stosuje się w obiegu zamkniętym. Owo ścierniwo dzieli się na grupy granulometryczne ze względu na rozmiar. Właśnie dzięki dokładnemu podziałowi na odpowiednie grupy granulometryczne uzyskujemy wysoką dokładność w procesie szkiełkowania. Mikrokulki dostępne są przykładowo w rozmiarach 100-200, 200-300 czy nawet 400-600 µm.
Dlaczego mikrokulki szklane są efektywne w szkiełkowaniu?
Stosowanie mikrokulek szklanych w procesie szkiełkowania niesie ze sobą szereg istotnych zalet, które wyróżniają je spośród innych rodzajów ścierniw. Po pierwsze, mikrokulki szklane charakteryzują się doskonałą jednorodnością i regularną strukturą, co przekłada się na precyzyjne i równomierne szlifowanie powierzchni. Ich twardość pozwala skutecznie usuwać nierówności, jednocześnie minimalizując ryzyko uszkodzeń obrabianego materiału.
Dodatkowo, mikrokulki szklane charakteryzują się bardzo wysoką odpornością na ścieranie, co przekłada się na długą żywotność ścierniwa i zminimalizowane zużycie w trakcie procesu szkiełkowania. To sprawia, że są ekonomicznym wyborem, przynosząc korzyści zarówno pod względem efektywności, jak i kosztów operacyjnych ze względu na fakt, że mamy do czynienia ze ścierniwem ekologicznym, dostępnym w niskich cenach. Zużycie mikrokulek szklanych jest odczuwalnie mniejsze niż np. zużycie piasku kwarcowego.
W porównaniu z innymi rodzajami ścierniw, takimi jak tlenek glinu, piasek kwarcowy czy krzemionka, mikrokulki szklane oferują także wyjątkową zdolność do kontroli rozmiaru i kształtu szlifu, co jest kluczowe w przypadku precyzyjnych zastosowań, na przykład w produkcji mikroelementów elektronicznych. Taki rodzaj ścierniwa jest również stosowany do obróbki mającej na celu ujednolicanie wyglądu powierzchni stalowych. Dzięki mikrokulkom szklanym uzyskujemy wysoką dokładność obróbki. Mamy również możliwość precyzyjnego wpływania na efekt wizualny obrabianej powierzchni.
Stosowanie mikrokulek szklanych może przynieść także korzyści środowiskowe, ponieważ szkło jest materiałem naturalnym i bezpiecznym dla środowiska. Pozwala również zachować większą czystość podczas pracy wpływając pozytywnie na obniżenie kosztów procesu czyszczenia. To zdecydowanie profesjonalne ścierniwo wielokrotnego użytku.
Sprawdź również nasz artykuł na temat Procesu Szkiełkowania
Wybór ścierniwa do szkiełkowania - na jakie szkiełko stawiać?
Szkiełkowanie polega na obrabianiu metalu, stali lub aluminium poprzez bombardowanie wybranej powierzchni strumieniem mikrokulek szklanych. Warto pamiętać jednak o tym, że samo ścierniwo musimy dobierać z uwzględnieniem właściwości powierzchni obrabianej. Ma to bowiem duży wpływ na skuteczność procesu.
Dobierając materiał ścierny w odpowiedni sposób możemy uzyskać wysoką dokładność i jakość oczyszczania oraz obróbki powierzchni metalowych. Jakie rodzaje mikrokulek szklanych można wykorzystywać w procesie szkiełkowania? Generalnie różnią się one głównie ze względu na swoją kulistość.
- Ścierniwo szklane kruszone - powszechnie oferowane mikrokulki szklane. Charakteryzują się ostro zakończonymi krawędziami, umożliwiającymi skuteczne usuwanie materiału z powierzchni metalu. Są używane do obróbki powierzchni w celu uzyskania odpowiedniego stopnia chropowatości.
- Ścierniwo szklane kuliste - to cząstki szklane o kulistym kształcie (cechujące się wysoką kulistością i czystością). Są stosowane w przypadku delikatniejszych powierzchni. Mają tendencję do bardziej równomiernego ścierania, co może być korzystne w niektórych zastosowaniach. Te najważniejsze to chociażby ujednolicanie wyglądu powierzchni (czyszczenia i uszlachetniania ze względu na regularny kształt) czy też szkiełkowanie delikatnego aluminium.
- Ścierniwo szklane cylindryczne - jest skuteczne w usuwaniu materiału z trudno dostępnych miejsc, takich jak otwory czy wgłębienia, zapewniając wysoką dokładność i jakość oczyszczenia. Jest również stosowane w przypadkach, gdy konieczne jest precyzyjne szlifowanie określonych obszarów (np. w motoryzacji - korpus silnika, karter, felgi itp.).
- Ścierniwo szklane mikrosferoidalne - jego kształt sprawia, że jest bardziej delikatne i nadaje się do zastosowania tam, gdzie wymagane jest bardzo precyzyjne szlifowanie. Ma znaczący wpływ na jakość wykończenia powierzchni - gdy chcemy postawić na matowienie, półmat lub też, gdy zamierzamy powierzchnię nabłyszczać czy chociażby satynować.
- Ścierniwo szklane do polerowania - często stosowane do końcowego etapu obróbki, ścierniwo szklane do polerowania ma za zadanie nadanie powierzchni metalowej gładkości i połysku. Jest to najdrobniejsze ścierniwo szklane. W znacznej mierze odpowiada za efekt wizualny obrabianej powierzchni po szkiełkowaniu.
- Ścierniwo szklane do usuwania rdzy - specjalne ścierniwo szklane jest czasem używane do usuwania rdzy z powierzchni metalu. Posiada właściwości, które pomagają w usuwaniu korozji i zabezpieczania obrabianej powierzchni przed jej dalszym postępowaniem.
Szkiełkowanie z użyciem szklanego granulatu
Proces szkiełkowania, choć pozornie prosty, wymaga starannego przygotowania i precyzyjnego wykonania. Jest on niezwykle zbliżony do procesu piaskowania, a kluczowym elementem jest odpowiednie przygotowanie stanowiska pracy oraz oczyszczenie powierzchni poddawanej obróbce. Dodatkowo, niezbędne są specjalne narzędzia (korzysta się często z pistoletów do piaskowania) oraz mikrokulki szklane, które pełnią rolę ekologicznego ścierniwa. Takie mikrokulki można zakupić chociażby w sklepach internetowych ze ścierniwami do piaskowania w zbiorczych opakowaniach (np. po 25 kg). Konieczne jest wykorzystanie takiej ilości, która zapewni optymalne wypełnienie pojemnika na ścierniwo.
Pierwszym krokiem w procesie szkiełkowania jest gruntowne oczyszczenie materiału, eliminujące wszelkie zanieczyszczenia, tłuszcze czy smary, które mogłyby negatywnie wpłynąć na jakość obróbki. Następnie, w zależności od potrzeb, dobiera się właściwy rozmiar kulek szklanych, które posłużą do przeprowadzenia procesu. To kluczowe, aby odpowiedni strumień ścierniwa, rozprowadzanego za pośrednictwem specjalnej głowicy połączonej z turbosprężarką, równomiernie ścierał obrabianą powierzchnię. W takiej sytuacji uzyskujemy wysoką dokładność i jakość obróbki.
Podczas procesu szkiełkowania, mikrokulki szklane są natryskiwane w mniej lub bardziej agresywny sposób (z mniejszą lub większą szybkością) na obrabianą powierzchnię. Ważne jest, aby stanowisko pracy było starannie zabezpieczone przed dostępem niepowołanych osób, co gwarantuje bezpieczny przebieg obróbki.
Po zakończeniu szkiełkowania, powierzchnia poddawana jest dokładnej kontroli jakości. Sprawdza się, czy uzyskano pożądany efekt chropowatej, półmatowej lub matowej struktury, eliminując wszelkie niepożądane defekty. Dodatkowo, powierzchnia jest starannie oczyszczana z pozostałości ścierniwa i zanieczyszczeń, co ma kluczowe znaczenie dla uniknięcia potencjalnych uszkodzeń czy korozji materiału w przyszłości.
W niektórych przypadkach konieczne może być dodatkowe zabezpieczenie powierzchni poprzez nałożenie warstwy lakieru, wosku lub innej substancji ochronnej, mającej chronić przed ewentualnymi uszkodzeniami czy korozją. W ten sposób proces szkiełkowania staje się kompleksowym działaniem, gwarantującym nie tylko estetyczny wygląd, ale również trwałość i jakość wykonanej obróbki.
Przyszłość szkiełkowania: trendy i innowacje
Szkiełkowanie to bardzo praktyczny sposób na obróbkę powierzchni wykonanych z metalu (i nie tylko!). Pozwala na precyzyjne oczyszczanie elementów, zmianę ich struktury i przygotowanie do dalszych prac. To zasługa unikalnych właściwości mikrokulek szklanych.
Ze względu na popularność omawianej metody z pewnością w jej przypadku w najbliższym czasie wprowadzane będą ciekawe innowacje - takie, jak chociażby udoskonalone narzędzia pozwalające na jeszcze bardziej efektywne przeprowadzanie procesu szkiełkowania. Na pewno pojawią się też próby automatyzacji pewnych procesów oraz nacisk na wdrażanie jeszcze bardziej doraźnych rozwiązań pro-ekologicznych.